Professional and high-quality metal alloys, ceramic products and concrete additives | RBOSCHCO
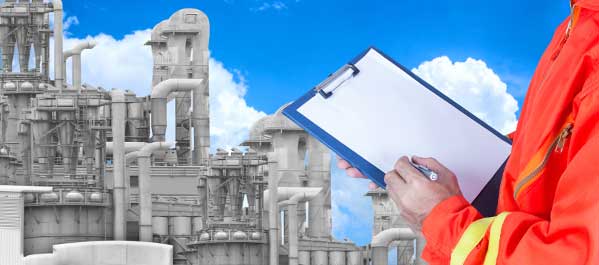
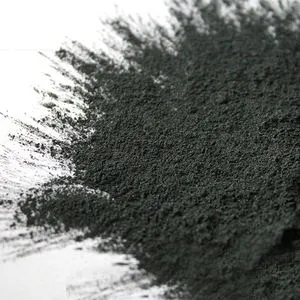
Why Choose RBOSCHCO?
KNOW MORE ABOUT US
As a leading nano-technology development and product applications additive manufacturer, RBOSCHCO dominates the markets. Tongrun technology provides solutions across the various processes and steps of laboratories and industries. Our professional working team provides the perfect solutions to help increase efficiency in various industries, create value, easy to deal with various challenges.
Concrete Admixtures
3D Printing Metal Powder
Liquid Chemicals
Powder Materials
SHOP BY CATEGORIES
Designed by artists, made by us, just for you.
BEST SELLER
FEATURED PRODUCTS
CUSTOMER REVIEWS
Words from Satisfied Shoppers
Latest News